- Home
- Popular products
- Jaw Coupling Types and Materials
Jaw Type Couplings, Inserts and Materials
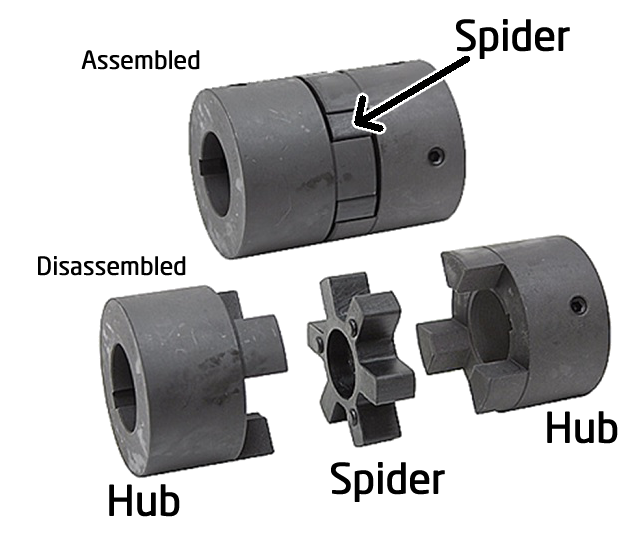
Basic Components
Characterized by its jaw-like hubs, Jaw type coupling serves many roles throughout various industrial environments, solely to transmit mechanical power produced from rotary motion via motor shafts. The Jaw coupling's primary components consist of two separated metal hubs with an spider-like insert fitted between. The hub’s design is cylindrical with protruding equally-spaced teeth and a central bore for attaching the shaft. Take note that the spacing between the teeth is also designed to accommodate the protrusions of the elastomer Spider (insert), which helps shield the components from metal on metal abrasion. Elastomer refers to polymers with elastic properties that of rubber. Thus an elastic Spider can suppress vibrations during operations, tolerate potential misalignments, and transmit Torque (the capacity to do work).
If the insert breaks down due to temperatures or physical conditions, the hubs' teeth will collide and remain interlocked, thus allowing the coupling to function without the Spider. Alternatively, Spiders made from rigid materials like oil-impregnated bronze to increase the coupling's torque, sacrificing speed (RPM) and operation versatility. Therefore, couplings with rigid Spiders are prone to wear down despite providing the most torque and couplings with soft Spiders sacrifice more torque for more protection.
Spiders eliminate the need for oil lubricants and its materials can be selected according to the environment or operational needs, and will last a long time under appropriate conditions. However, the elastic nature of the Spider means it will begin to compress permanently, and it is highly advised to replace a Spider by the time it reaches 75% of its initial thickness.
Insert designs offer their own benefits and drawbacks
- Solid Center (A): Solid center Spiders can be used to prevent the two connected motor shafts from phyiscally touching. Less positioning capabilities but provides the most optimal RPM.
- Open Center (B): Conversley, sacrificing RPM for more shaft postioning is only feasible with an open Spider design. This design allows the two shafts the utilize the most space.
- Cushion (C): Cushions are not necessarily Spiders, but serves the same purpose as any elastomer. Cushion sets are fitted to larger medium to heavy-duty Jaw type coupling, and additionally needs a collar to secure the components all together.
- Flexible (D): Similar to the open center design, but the Spider can be radially attached or removed from the coupling without affecting the hub components. Its design allows it to be snapped together and secured with a retaining ring or collar. Flexible Spiders have a limited material pool to select from due to the nature of its design.
- Round-tooth (E): Straight tooth Spiders are designed for accuracy during movement, whereas curved tooth Spiders are ideal for precise start and stop operations found in servos or other motion control systems. In-shear spiders are designed to prevent continued operations in case of insert failure.
- In-shear (F): In-shear Spiders provide ample space between hubs, preventing them from interlocking and producing any torque if the Spider fails. These variations are typically secure its components with a In-shear ring.
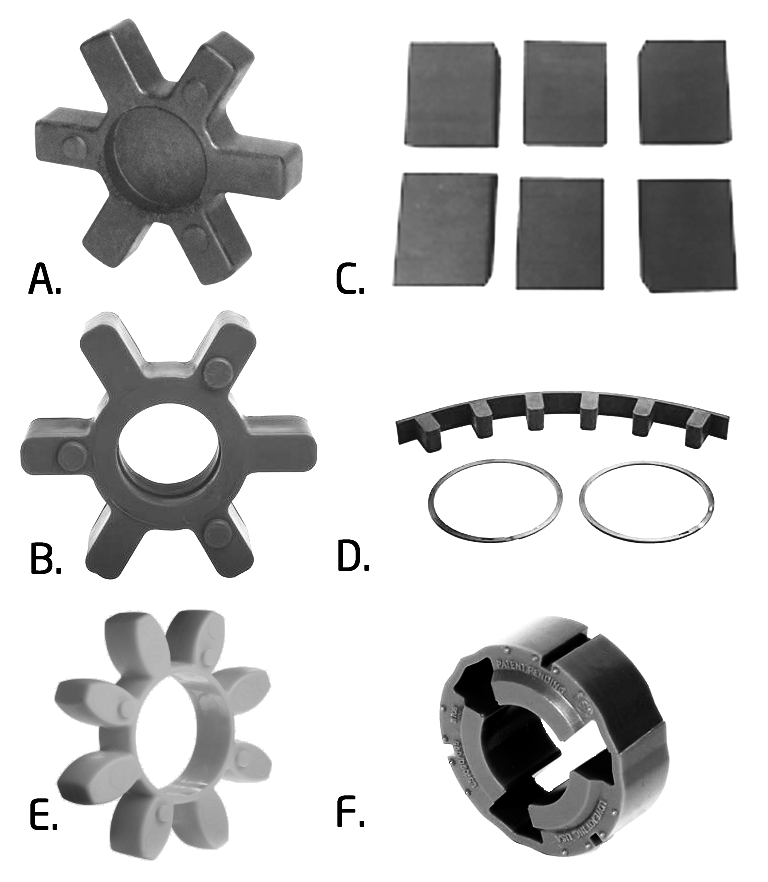
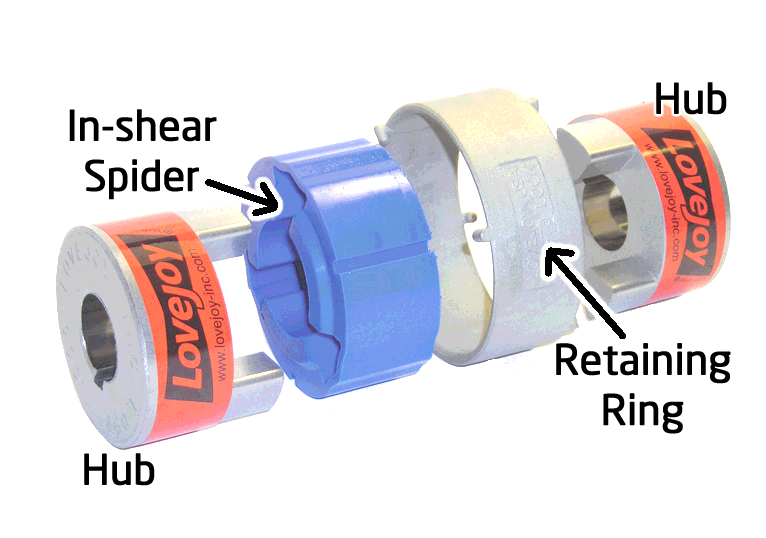
In-shear type coupling excels at preventing any equipment damage if insert failure occurs. Typical Spiders that do fail will result with metal on metal collision and abrasion, utlimately resulting in required maintenance in the future. The Jaw hubs of In-shear type coupling only interlace with an In-shear Spider that bridges the two hubs together. In-shear Spiders can be radially attached or removed much like its flexible cousin (D) and additionally has grooves so the steel ring to slide into place, securing the components completely if properly installed. Since the In-shear Spider is also radially attachable, it does suffer from the limits of materials it can be made from. Despite this limitation, the In-shear coupling still remains popular for a wide range of applications.
Spider Materials Comparison
Name | Torque (in-lb) |
Dampening Capacity |
Rotations per Minute (RPM) |
HP/100 RPM |
Temperature Range |
Resistances | ||||
---|---|---|---|---|---|---|---|---|---|---|
Min. ˚F |
Max. ˚F |
Min. ˚C |
Max. ˚C |
Oil | Chem. Rating |
|||||
|
|
|
|
|
|
|
|
|
|
|
|
|
|
|
|
|
|
|
|
|
|
|
|
|
|
|
|
|
|
|
|
|
|
|
|
|
|
|
|
|
|
|
|
|
|
|
|
|
|
|
|
|
|
|
|
|
|
|
|
|
|
|
|
|
|
★ Self-lubricating bronze (Oilite)
Materials that offer more torque capacity trend to be more rigid, and excel at reducing backlash that would otherwise be experienced from a standard elastomer. However, the trade-off is the potential wear and maintenance that will be required if a rigid spider is chosen. Higher-grade materials like hytrel will still face limitations if operation conditions require repetitive or sudden activity. Standard elastic materials like Buna N rubber are well suited to protect components under rigorous activity. Thus, it is important to understand the trade-off between materials and its potential applications. It is also important to consider the spider's design since it can also influence the material choices, Flexible and In-shear designs are limited to Buna N and Urethane, whereas Cushion sets are limited to Buna N, Bronze and Hytrel.
Insert designs and materials are just the tip of the iceberg of Jaw-type coupling. Knowing what sizes, designs, and materials for Jaw coupling really boils down to practical knowledge and relying documentation for the best applications of said components. Additionally, Jaw-type coupling installation is whole other beast to be slain, requiring utmost patience, preparation and attention to details for maintenance free results. Materials and Spider designs can accomodate for misalignment, but the margin of misalignment is still limited by their respective materials and designs, etc. Therefore, the best practice is to read the documentation, and keep it available to you at all times!