Seals
Seals play a primary role in the performance and longevity of industrial machinery. As integral components, they prevent the escape of fluids and gases from machinery, maintaining optimal pressure and temperature. They shield sensitive parts from external contaminants like dirt and moisture, enhancing the machinery's durability. By mitigating friction and wear, seals contribute to industrial machinery's smooth operation and energy efficiency, significantly impacting productivity.
Seals BY CATEGORY
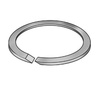
Back-Up Rings
Used in conjunction with O-rings or other sealing elements to provide additional support, enhancing the sealing performance and longevity of seals in high-pressure applications.
Show Back-Up Rings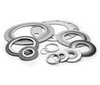
Gaskets
Components used to create a seal between two or more mating surfaces, preventing leaking of fluids or gases in various applications.
Show Gaskets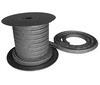
Packing Seals
Utilized in industrial settings to create a tight and secure seal between components in harsh operating conditions.
Show Packing Seals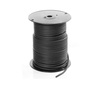
Extruded Cord
Made from polymers or rubber, used in various applications such as sealings and gaskets, offering versatility and durability.
Show Extruded Cord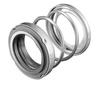
Mechanical Seals
Prevents leakage between rotating shafts and stationary parts by utilizing a combination of stationary and rotating components.
Show Mechanical Seals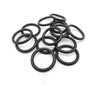
O-Rings
Circular sealing devices made from elastomeric materials, used in industrial and mechanical applications to create a reliable and leak-proof seal between mating surfaces.
Show O-Rings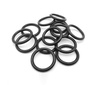
Oil Seals
Prevent the leakage of lubricants, oils, or fluids in rotating or reciprocating machinery, providing a barrier between moving parts and the external environment, ensuring proper lubrication.
Show Oil Seals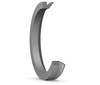
V-Rings
Designed with a V-shaped cross-section for effective sealing against contaminants in rotating shafts and dynamic sealing applications.
Show V-Rings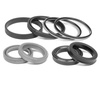
Other Seals and Seal Kits
Various sealing components provide reliable sealing solutions for specific requirements such as high temperatures, aggressive chemicals, or extreme pressures.
Show Other Seals and Seal Kits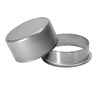
Shaft Repair Sleeves / Wear Sleeves
Components used to repair and restore damaged or worn shaft surfaces.
Show Shaft Repair Sleeves / Wear Sleeves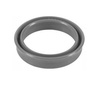
Rod and Piston Seals
Sealing devices used in hydraulic and pneumatic systems to prevent fluid leakage along the reciprocating motion of rods or pistons, providing a reliable seal between the moving component, ensuring efficient operation.
Show Rod and Piston SealsSeals POPULAR PRODUCTS
Martin Sprocket CSW6 3" WASTE PACK SEAL
Brand Martin Sprocket
Model CSW6
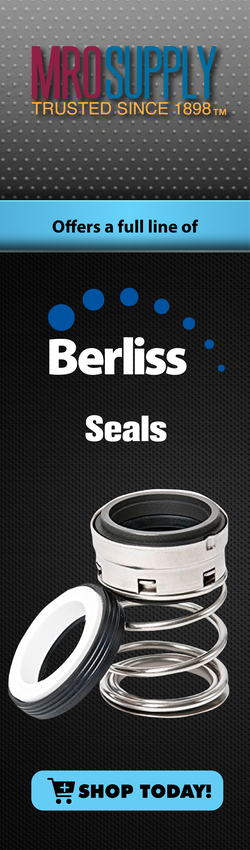
About Seals
Industrial seals are essential in various machinery and equipment, and the types of seals are diverse, each with a specific purpose. O-rings, for instance, are simple and versatile, providing sealing solutions for many applications. Mechanical seals are commonly used in pumps to prevent fluid leaks. Gasket seals cater to irregularities between mating surfaces, while oil seals retain lubricants and exclude dirt and moisture. Shaft repair sleeves repair worn shaft surfaces, while rod and piston seals suit high-pressure, reciprocating movements, such as those in hydraulic cylinders.
Gaskets create seals between two surfaces, preventing leaks and maintaining pressure in various systems. They seal the junction between a cylinder head and an engine block in automotive applications, and they ensure airtight seals in pipe joints and prevent water leakage in plumbing. Also, gaskets provide electrical insulation and heat resistance in the electronics industry. Their versatility and reliability make them indispensable in several industrial applications.
Mechanical seals are crucial components in various machinery, especially those involving pumps and rotating equipment. They primarily prevent fluid leakage into the external environment, ensuring efficiency and safety. These seals help maintain pressure, control temperature, and even enhance the durability of the machinery, playing an indispensable role in industrial processes.
O-rings have many applications in various industries because of their simple yet effective design. These elastic loops, typically made of rubber or other pliable materials, play a crucial role in sealing connections in machinery to prevent the leakage of gases or fluids. O-rings are essential in hydraulic and pneumatic systems, automotive applications, and even aerospace technology, where they ensure the integrity of fuel and propulsion systems.
Oil seals, or shaft seals, are essential in various industrial applications. These mechanical components prevent the leakage of oils, lubricants, or other fluids from bearings while simultaneously preventing external contamination. As protective barriers, they are critical for ensuring the efficiency and longevity of machinery and equipment. Additionally, oil seals help uphold the operational integrity of systems by ensuring lubricants remain within the bearings, which reduces friction, wear, and tear.
MRO Supply offers a complete inventory of seals, including back-up rings, V-rings, extruded cords, and packing seals. Our products come from only the most reputable manufacturers so that you can count on MRO as your one-stop shop for seals.
Seals BLOGS
View all blogsBolt Tightening Sequence: Why it is So Important in Industrial...
If you have an industrial facility where operations involve dealing with shafts, flanges, and bearings,...Sprockets Diagnosis: What are the Common Problems?
When checking the alignment, it is also good to review the state of the sprocket, seals, and bearings.Five Factors to Consider when Choosing Hydraulic Fittings
Hydraulic systems have been evolving rather fast as engineers work on variations to deliver higher efficiency.Do Not Let Your Bearing Down: Halt Corrosion before It Starts
Do not let your bearing down; here is what you should do.