- Home
- Popular products
- Lubrication for Plain and Roller Bearings
Lubrication for Plain and Roller Bearings
Bearings can be found in many industrial applications. Their ability to encourage rotary motion is useful for turbines, compressors, and other similar shaft-driven technology. Bearings also serve as a crucial supporting mechanism for the shaft, which withstands constant load stress during performance. Lubrication plays a major role providing bearings the ability to support the main shaft and enhance the sliding ability between bearing and shaft surfaces. There are lube-free bearings that are used in industry, but they have limited applications and can be quite costly as well. Bearings that do rely on lubricant to achieve this behavior can vary between the methods of application, and external systems, while expenseive, can be installed installed to automate lubricant distribution.
However, the more common bearings, such as the plain and roller bearings can be comparatively inexpensive and last for quite some time. Plain bearings are made with enough clearance between the shaft and the bearing's lining to allow lubricant to perform hydrodynamically. Roller bearings on the other hand use lubricant alongisde its rolling elements elastohydrodynamically. These are considered ideal behaviors between bearings and lubricant, since hydrodynamic or elastohydrodynamic behaviors can protect the machine components and support the more valuable shaft. These are in fact two of the four behaviors that are formally referred as lubrication regimes, and I will be discussing about what happens during these regimes. I will also dive into the advantages and disadvantages of lubricant types, and which of these suit the bearing type.
Lubrication Regimes
What are lubrication regimes? I first mentioned them being behaviors, but we can also think of them as a stage in a spectrum that characterizes how the lubricant interacts with the bearing. The regimes reflect the ability to produce a fluid film from the lubricant. Fluid film is important for preventing wear and damages, and allowing sliding motion. This is because fluid film is like a strong liquid barrier, but it can only be made under certain conditions. Pressure, speed, and lubricant viscosity all play an important role in formulating the fluid film. All four regimes influences these properties differently and not all them can produce fluid film as a result. It is important to understand lubrication regimes because they reveal how lubricant changes thoughout operations and help us diagnose the source of wear within bearings.
Boundary regime is when the lubricated surfaces of the shaft and the bearing's lining produces metal on metal contact, likely resulting in abrasion. Abrasion describes the kind of wear or gradual damage that occurs when two surfaces slide and resist each other. Constant surface contact builds up damage to the bearing and shaft, which will eventually result in component failure. Conditions must be improved to prevent boundary regime behavior. Boundary regime occurs during startup/shutdown phases, when the shaft is rotating at low speeds, or when the shaft is withstanding high loads.The lack of speed in rotation fails to produce enough pressure to form the fluid film. In order to accommodate for boundary regime, using a lubricant with an appropriate viscosity might help reduce wear. If viscosity or stickiness is too low, the lubricant will not be able to produce an oil layer. Too high increases friction and temperatures, resulting in energy loss. Lubricants can also be improved with special additives in the mixture, like specific ones that can create a protective layer that can be worn down instead.
Mixed regime exihibits a mix of behaviors found in hydrodynamic and boundary regimes. Mixed regime can be considered as a transition between the two regimes. As shaft speed builds, the pressure wedge of lubricant begins to form fluid film, but is never fully formed. Surface contact occurs briefly because the lubricant layer is trying to form and lift the shaft from the bearing surface.
Hydrodynamic regime is when the fluid film is successfully formed and is separating the bearing and shaft surfaces from each other. It is the most optimal regime for extending the lifespan of bearings and shafts. Many factors play into maintaing hydrodynamic behavior like lubricant viscosity and shaft speeds. However, conformity is how two surfaces relatively matches their curve with one another, and surfaces that conform well will better succeed at forming fluid film. Imperfections will increase temperatures and cause other unsual behaviors instead.
Elastohydrodynamic regime is very much like hydrodynamic regimes but this regime deforms metal surfaces elastically as a result of low surface conformity. Bearings with low surface conformity will cause the lubricant flow to roll, consequently creating brief high pressures at the contact points. High pressures produce dense film with increased viscosity and load capacity, quite capable of briefly deforming metal before returning to its original state. The conditions to maintain elastohydrodynamic regimes are finicky but can prevent abrasions if done right. This regime is especially prominent in bearings that lack smooth surfaces: rolling element bearings, toothed bearings, etc.
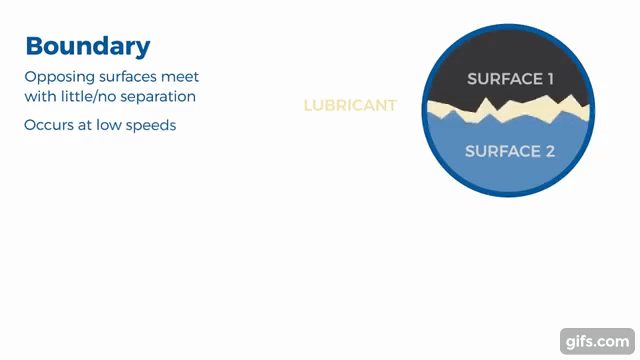
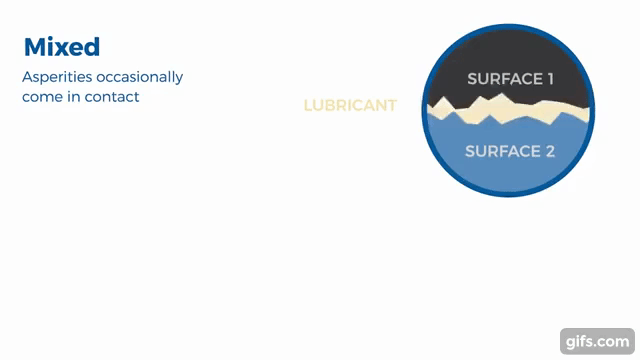
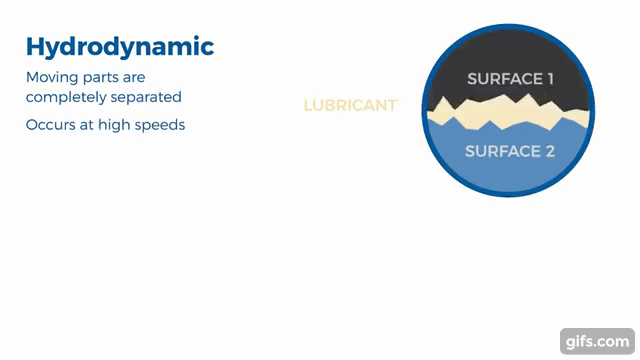
Oil vs Grease
As stated earlier, lubricant can enhance sliding ability and help protect surfaces from wear. Lubricant can also be enhanced with additives and thickeners that can accommodate almost an operating needs.
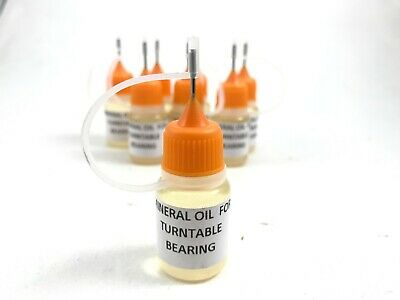
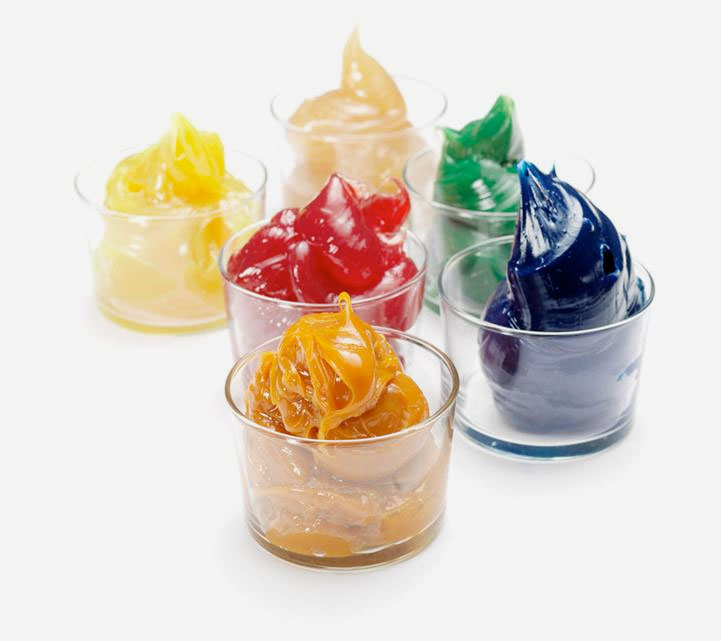
Oil serves as the base of the lubricant mixture. Types of oils range from:
- Mineral oil
- Polyalphaolefin
- Ester oil
- Polyglycol
- Silicon oil
- Perfluoroalkylether
Thickener allows the mixture to become more like a grease, which allows the mixture to retain and distributes oil over time. Types of thickeners range from:
- Metal soap
- Polyurea
- Gel
- Teflon
Additives grant bonus chemical properties to the mixture that can help improve the bearing's performance or other beneficial behaviors such as:
- Corrosion resistance
- Chemically induced layers for wear protection
- Controlling viscosity
- Aging and oxidizing prevention
Compared to greases, oils do not suffer from the drag of being a solid mass. Bearings and shaft systems greatly benefit from the liquid nature of oil - lubricating multiple machine components efficiently and having the added benefit removing heat. Oils can use oil inlets as a reliable entry point into shaft systems, and can also use oil outlets if needed to be drained. However, being a liquid means that oil can leak and possibly endanger systems that not resistant to oil. Leakage issues can be solved by simply adjusting for an ideal oil level. This can be done routinely by hand, or advanced systems can be installed to provide excesss-free amounts of oil automatically. The latter is the more expensive option, but could save shaft systems from any human errors.
Greases should only be used for bearings that can alllow it. Premade greases and greases made from thickener form a solid mass. There are benefits and disadvantages to use grease over oil, but oil is more commonly preferrred. The unique thing about grease is that it stores and then releases oils over time. Lubricant used this way lasts longer and less expensive as a result. Grease can also act as a seal for fitted components. However, grease is much harder to supply over time unless their are systems that can supply grease through a special inlet. Older grease will also begin to oxidize and solidify completely which must be avoided. Cleaning and removing grease can also be quite the chore - newly added grease needs to be able to force out older grease if being supplied externally. Extreme cold or hot temperatures also can cause a lot of issues for grease, so it might be wiser to rely on oil unless you are prepared to invest in the more expensive greases.
Plain Bearing Applications
Plain bearings are the simplest in design, using a basic sleeve with bearing lining as the primary supporting element to the shaft. They are excellent for supporting heavy-duty operations like turbines, compressors, gearboxes and such with their massive load capacity. This is largely thanks to its conformity to the shaft surface and the ample amount of clearance for the lubricant to enter. These conditions help produce fluid film more efficiently due to a lack of imperfections. Plain bearings make the most use from oil lubricants since they are easy to administer through oil inlets. Some bearings are even designed with grooves for the oil to travel and lubricate as the shaft is rotating. Plain bearings also features grease nipple connectors for grease guns. Upon connection, the grease is drawn out from the gun and into the inner valve-like mechanism of nipple.

Rolling Element Bearing Applications
Rolling element bearings are comparatively more intricate than their "plain" counterparts but are very useful when operating loads aren't as demanding. These bearings are commonly designed with inner and outer races for rolling elements to travel along - rollings element can come in different types: ball, roller, needle-roller, and tapered bearings. Rolling elements are spherical or cylindrical in shape, minimizing surface contact and reducing friction simultaneously. However, cages can used to control spacing between elements, but can also restrict elements and increase friction. Roller bearings feature plenty of clearance for lubricant, and can also effectively use grease under suitable temperatures. Adding too much grease forces the inner elements to churn through the lubricant, increasing friction and temperatures. As long as the lubricant is kept contamination-free and at controlled amounts, roller bearings will last much longer in industry.
Conclusion
This article was a brief look at the many interactions of lubricant in bearings. It is mixture that can be modified to suit any bearing's needs, but only if not neglected. Operating conditions are never perfect, and can adversely affect your shaft systems if not properly accounted for. Otherwise, consider lubricant free bearings and where they would best apply in industry.
Image Credits
- Bearing Lubrication Monitoring with Ultrasound SDT, https://sdtultrasound.com/industry/bearing-lubrication-monitoring/
- What are Lubrication Regimes? Nye Lubricants, https://www.nyelubricants.com/what-are-lubrication-regimes
- GREASES GAMCO, https://gamco-agency.com/greases
- High Performance Lubricants Cortec Corporation, http://presservbrasil.com.br/upload/catalogos/Lubricants_PresservBrasil.pdf
- Too Much or Too Little Lubricant: Which Is the Bigger Problem? Machinery Lubrication, https://www.machinerylubrication.com/Read/31806/too-much-little-lubricant
- 8 Lubrication Failure Mechanisms for Rolling-element Bearings Machinery Lubrication, https://www.machinerylubrication.com/Read/31068/bearing-failure-mechanisms